Compressed air systems are integral parts of many manufacturing facilities across a range of industries including automotive, pharmaceutical, electronics, assembly, food processing, and many others. These systems convert power into potential energy stored in pressurized air, which is then utilized to drive machinery, tools, and processes essential for production and maintenance. Understanding the basics of compressed air systems is crucial for optimizing performance, ensuring safety, and reducing operational costs. The following content provides an introduction to compressed air systems, including the compressors, piping materials, valves, dryers, and filters.
What is Compressed Air?
Compressed Air is air that is pressurized to greater than atmospheric pressure. It is similar to air that you breathe, but has been forced to smaller volume and kept under pressure. It is Made of 78% Nitrogen, 20-21% oxygen and 1-2% of other gases. Compressed air can be stored at high pressure and is a great (and expensive) medium for transmitting energy. Its typical operating pressure is 100-120 psi.
Compressed air has many uses, including:
- Pneumatic Tools
- Manufacturing Facilities (Drying / Blow-off, Actuation, Sandblasting, Conveying)
- Humidification
- Medical Air (Surgical Tools, Inhaled Medication, Ventilators)
- Building Automation
Components of Compressed Air Systems
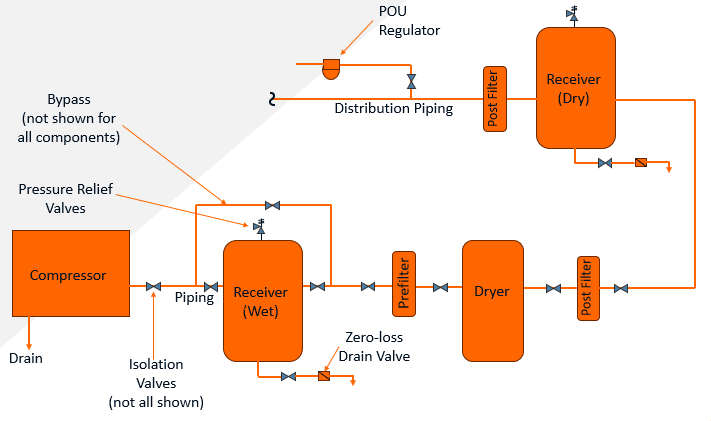
There are several different kinds of compressors, choosing which type depends on requirements including flow, air quality, demand profile, and cost. The primary types of compressors are:
- Reciprocating
- Rotary Screw
- Centrifugal
- Scroll
Reciprocating Compressors
Reciprocating Compressors are positive-displacement machines that use a piston to compress a gas and deliver it at high pressure.
Advantages:
- Used to produce higher pressure
- Flexibility – Oil/Oil free
- High efficiency
- Durability and low maintenance cost
Disadvantages:
- Sizing
- Noise
- Not able to self-regulate
- Temperature of air outlet is very high
Rotary Screw
These compressors use a rotary positive displacement mechanism comprised of helical gears (screws) to compress air by reducing the volume of a chamber. They deliver a constant stream of compressed air and are 100% duty machines.
Advantages:
- Continuous duty cycle, no pulsation.
- Noise level
- High air flow delivery
- Compact Size
- Oil flooded/Oil Free
Disadvantages:
- High initial cost
- Not ideal for intermittent loads
- Maintenance is less frequent but more complicated
Centrifugal
Centrifugal compressors convert energy utilizing a series of stages to compress and cool the air as it continuously flows through the unit.
Advantages:
- Can handle large volumes of gas at high flow rates
- High efficiency and require less energy to operate
- Compact size
- Good for high constant flow
Disadvantages:
- High initial cost compared to other compressors
- Require specialized maintenance
- Limited turndown capability and may not be suitable for applications that require variable flow rates
Oil-less, Oil-free, or Oil Flooded?
- Oil-less
- Often medical grade
- Oil-free
- Common in clean manufacturing processes
- Semiconductor, food, pharma, electronics
- Oil Flooded
- General shop air
- Food
Oil Flooded compressors can produce oil-free air with appropriate filtration. However there is risk of oil contamination if components fail.
Capacity
Sizing is not necessarily straightforward, but these considerations are necessary:
- Need to establish an assumed diversity
- 40%-50% diversity usually is conservative
- Take into account altitude derating
Variable Speed Drive (VSD) vs Fixed Speed
VSD will more effectively accommodate changes in demand and will typically more energy efficient. However VSD is more expensive than fixed speed. VSD will control pressure setpoint more accurately. For a multiple compressor system, you can have fixed speed for base load and VSD for trim.
Air-Cooled vs Water-Cooled
Choosing between air-cooled and water-cooled chillers will depend heavily on what is being cooled. Small compressors will be air cooled.
If chilled water is available, water cooled is generally better, especially for low dewpoint requirements. Heat to space for air cooled can be large, heat to space for water cooled is less, but still significant.
For more information on chillers, check out our blog post here.
Compressor Air Piping Materials
Carbon Steel
- Acceptable for “dirty” air
- Do not use in any clean applications
- Typically threaded
Copper
- Most common
- Usually soldered or brazed
- Compression for smaller piping (3/4” and below) at drops
- Starting to see some pro-press systems
Stainless Steel
- Not common outside of semiconductor and other clean processes
- Sometimes used in lieu of copper for large sizes ~6” and above
- Usually welded at larger sizes
- Compression for smaller piping for drops
- Can use victualic
- Different types of piping
- Schedule 10 or 40 pipe
- A269 Tubing
Aluminum
- Specialty” product engineered for compressed air
- Mechanical fittings
- Powder coated pipe, better corrosion resistance than copper
- Same joining method available in stainless steel
Plastic
- Never use PVC or CPVC for compressed air piping
- ABS (Acrylonitrile Butadiene Styrene) is allowed for compressed air piping. It has a much lower allowable pressure than metallic pipe
CFOS (Cleaned For Oxygen Service) is required for medical, semiconductor, laboratory, and other clean applications. Copper, Stainless Steel, and Aluminum are available in CFOS.
Valves
Ball Valves
- 2 or 2 ½” and under
- Full port
- 2 or 3 piece construction
- Medical air allows only 3 piece ball valves
Butterfly Valves
- 2 ½” or 3” and over
- Full lug style
- Dead end service
- Ductile iron bodies, may need coating or liner for clean applications
- Stainless steel and double offset available
Check Valves
- Very uncommon in compressed air systems
- Not required in most cases when compressors are headered
- Compressor usually has internal check
- Adding external check can be detrimental
Condensate Management
Condensate is generated in several places including compressor, dryer, receiver tanks, filters, and low points in piping. Condensate needs to be disposed of, so make sure you have floor sinks at compressed air equipment like automated condensate drain valves. Automatic condensate drain valves can have an electronic timer, or zero loss drain valves. Electronic valves use a solenoid that opens at a set interval for short amount of time. This can waste compressed air. Zero Loss Drain Valves include electronic and pneumatic floats, which minimize waste of compressed air.
Auto drain valves can be in the following locations:
- At discharge of compressor
- At wet receiver, optional at dry receiver
- Usually not required at compressor and dryer drains
- Filters can usually be specified to have auto drain valve built in
- Low points in piping
- At header
- Usually not in distribution piping
Dryers
Dryers remove moisture from the air, so it is important to know the dewpoint requirement to decide the dryer type.
Refrigerated Dryers
- Dewpoint down to ~38-45 deg F
- Be aware of deratings for ambient and inlet conditions
- Warmer/more humid air will result in derating and a higher discharge dewpoint
- Need to consider heat rejection to space, usually air cooled
- Be aware of location of ambient air inlet/outlets on dryers relative to compressor. Do not want the hot air from the dryer going into the inlet of the compressor
Desiccant Dryers
- Compressed air passes thru desiccant media
- Required for lower dewpoints, down to -100 deg F
- Dual towers, one active while other is regenerating or idle
- Desiccant is regenerated either using compressed air (heatless) or heated blower air (heated)
- Heatless Dryers can use a significant % of compressor output for regeneration, up to 20%
- Need to consider when sizing compressor
- Heated Regeneration
- Uses a separate blower and heater to regenerate desiccant
- Less parasitic use of compressed air, but still may be present
- Can produce swings in dewpoint during regeneration cycle
- Clarify with manufacturer when specifying
- Temperatures can get HOT up to 350 deg F
- May need to pipe regeneration air outside
- Have had trouble getting flow rate of blower from vendors
- Typically blower will only support very small pressure drop
- Recent project – 0.1 psi
- Need to calculate pressure drop to discharge point and upsize pipe if needed
- Consider thermal expansion
- Insulate pipe and dryer
Filtration
Filters address moisture, oil, and particles. Pre-Filter required prior to dryer, and post filterafter dryer.
Oil Water Separators
These are used to separate oil oil from condensate and are required for oil filled systems. Condensate from compressors, receivers, filter, etc are piped to Oil Water Separators. OWS depressurizes and separates oil. Clean condensate is drained to sanitary sewer.
Receiver Tanks
Receiver tanks provide system capacitance. They are typically part of compressor package for reciprocating compressors, and can be part of package for smaller rotary screw.
Typical Sizing:
- 1.25 x CFM = size of tank in gallons
- 1.5 x CFM = size of tank in gallons
- V=t*C*Pa/(P1-P2)
- V=volume of tank in gallons
- t=time for receiver to go from upper to lower pressure
- C=flow required
- Pa=atmospheric pressure
- P1=max tank pressure
- P2=min tank pressure
Oversizing Wet receiver can overflow dryer causing dewpoint spike
Ultimately, compressed air systems are vital to a wide range of industries, providing the necessary power to drive tools, machinery, and various processes essential for production and maintenance. From the fundamental components like compressors and piping materials to specific elements such as valves and filtration units, understanding each aspect is crucial for optimizing performance, ensuring safety, and reducing operational costs. By selecting the appropriate compressor type, managing condensate effectively, and ensuring proper filtration and dryer systems, industries can maximize the efficiency and longevity of their compressed air systems, contributing to smoother operation.