In the world of facilities management, making informed decisions is key to ensuring the long-term success and sustainability of any project. One of the most effective tools for achieving this is a Life Cycle Cost Analysis (LCCA), a powerful methodology that evaluates the total cost of ownership of a facility or system, considering all expenses from initial design and construction to operation, maintenance, and eventual disposal or replacement. The concept of life cycle analyses is widely accepted in the AEC industry; a recent example is the Association of Physical Plant Administrator’s development of the APPA 1000 Standard “Total Cost of Ownership for Facilities Asset Management”. This concept holds especially true for MEP Systems, which are the backbone of any building but also incur the most operational cost. Making thoughtful evaluations about these systems are critical to the long-term success of a facility.
EEA was founded as “Energy Engineering Associates” and has held a primary focus on energy conservation and sustainable design since 1977. Because our roots are in energy conservation analysis and retrofit design, our staff has extensive knowledge and expertise in energy-efficient systems design, equipment selection and specification, and control strategy application and optimization.
Our typical workflow considers analysis in early design phases and is a persistent sounding-board through value-engineering and into construction. When developing system or whole-building energy models (commonly on high-performance building designs), we consider system and building life cycle when performing individual and combined parametric simulations, providing designers and owners with a menu of options for high performance results. We set ourselves apart from our peers by establishing the fundamental bottom-line understanding and purpose of each project’s analysis and do not treat the process as a simple compliance process. This method has produced a repeatable and scientific approach to energy, carbon, and water savings – with tremendous benefit for our clients.
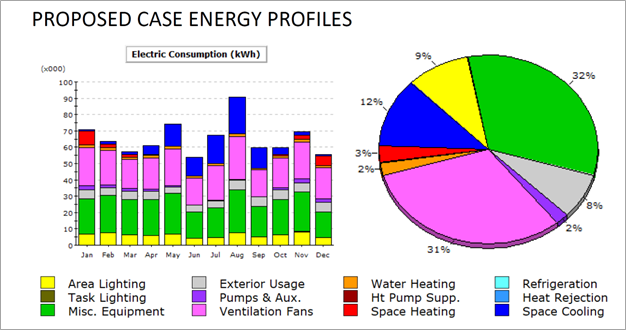
Building Energy Model Energy Use Output
But what happens when the Life Cycle Cost Analysis process is overlooked? What are the implications for facilities and their management teams? In this blog post, we’ll delve into the importance of LCCA, what can go wrong without it, and how it is applied in practice.
The Importance of Life Cycle Cost Analysis
- Comprehensive Cost Evaluation: A LCCA provides a detailed analysis of the total costs associated with a facility over its entire life span, considering not just the initial purchase price but also the ongoing operational and maintenance costs. This ensures that decisions are made based on the true long-term value of the systems.
- Enhanced Performance and Reliability: By factoring in the total cost of ownership, a LCCA encourages the selection of MEP systems that offer better performance and reliability over time. This helps in minimizing unexpected breakdowns and maintenance needs, ensuring that the systems operate smoothly throughout their life cycle.
- Energy Efficiency and Sustainability: A LCCA plays a critical role in promoting energy efficiency and sustainability. By evaluating the long-term costs of energy consumption and potential savings from more efficient technologies, a LCCA helps facilities managers choose systems that reduce energy use and lower the facility’s overall environmental impact.
- Optimal Resource Allocation: With a LCCA, facilities managers can allocate resources more effectively by identifying which systems offer the best return on investment over time. This ensures that funds are spent on systems that provide the most value, rather than on short-term savings that may lead to higher costs in the long run.
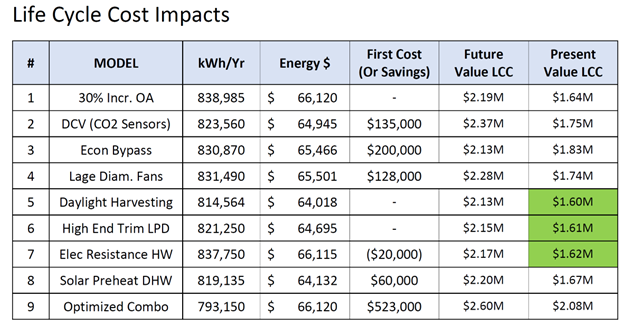
Energy Conservation Measure LCCA Summary
The Consequences of Skipping Life Cycle Cost Analysis
When a LCCA is not performed, the decisions made during the design and construction phases can lead to significant and often unforeseen costs later on. Here’s what might happen:
- Escalating Operational Costs: Without a LCCA, choices made in the early stages of a project may prioritize lower upfront costs without considering the long-term expenses of maintenance, energy use, or repairs. This often leads to higher operational costs over the facility’s lifespan, as cheaper materials or inefficient systems require more frequent repairs or consume more energy.
- Premature System Failures: Facilities that are not designed with their full life cycle in mind may suffer from premature failures of critical systems. For example, opting for a less expensive HVAC system without considering its long-term reliability and maintenance needs could result in costly breakdowns and replacements far sooner than anticipated.
- Budget Overruns: Projects that don’t incorporate a LCCA are more likely to experience budget overruns in the long run. Unanticipated repairs, higher energy bills, and the need for early replacement of components can strain budgets and reduce the financial viability of the facility.
- Missed Opportunities for Sustainability: MEP systems are key contributors to a facility’s energy consumption and environmental impact. Without a LCCA, opportunities to invest in more sustainable, energy-efficient technologies may be missed, resulting in higher energy costs and a larger carbon footprint.
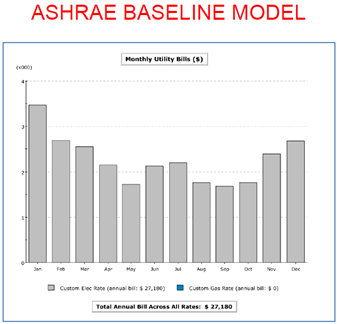
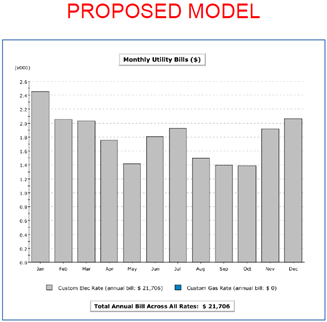
Building Energy Model Monthly Consumption Comparison
Applications of Life Cycle Cost Analysis
LCCAs are widely used across various stages of a facility’s life and can be applied to:
- Design and Construction: During the planning phase, a LCCA helps in selecting materials, systems, and designs that offer the best value over the facility’s life span. For example, it might show that investing in a more expensive roofing material will save money over time due to its longevity and lower maintenance needs. For this reason, LCCAs are commonly used, and sometimes required, in the design process for high-performance buildings.
- Energy Efficiency Projects: A LCCA is crucial in evaluating energy efficiency projects. It helps facilities managers compare the costs and benefits of different energy-saving technologies, such as upgrading to LED lighting or installing solar panels, ensuring that the chosen solution offers the best return on investment over time. LCCAs are frequently used as a tool to assist in justifying energy conservation measures or retro-commissioning projects. For our San Antonio Water System Heating and Cooling Assessment, a LCCA confirmed that decentralizing the existing downtown steam distribution system would result in significant energy and water savings for the Utility and its customers.
- Maintenance Planning: A LCCA can inform maintenance strategies by identifying which components of a facility are likely to incur the highest costs of ownership over time. This enables proactive maintenance and replacement planning, reducing the risk of unexpected failures and associated costs by running to failure.
4. Asset Replacement: When it comes to the time to replace major systems or equipment, a LCCA guides decision-makers in choosing options that minimize long-term costs. For instance, when replacing an aging HVAC system, a LCCA can help compare the total cost of ownership of different models, considering factors like energy efficiency, maintenance needs, and expected lifespan. This concept can apply to whole-system renovations, but also initial selection or replacement of large single components. For example, we often perform LCCAs for large capacity water cooled chiller installations, considering factors such as full and part load efficiency, constant or variable speed operation, optimal design conditions, and equipment voltage. This process was used to establish the basis of design chillers for our 10,000-ton Austin Energy District Cooling Plant #3 project.
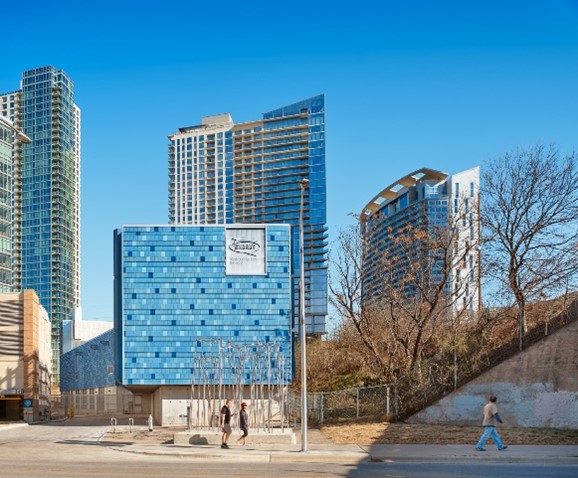
Austin Energy District Cooling Plant #3
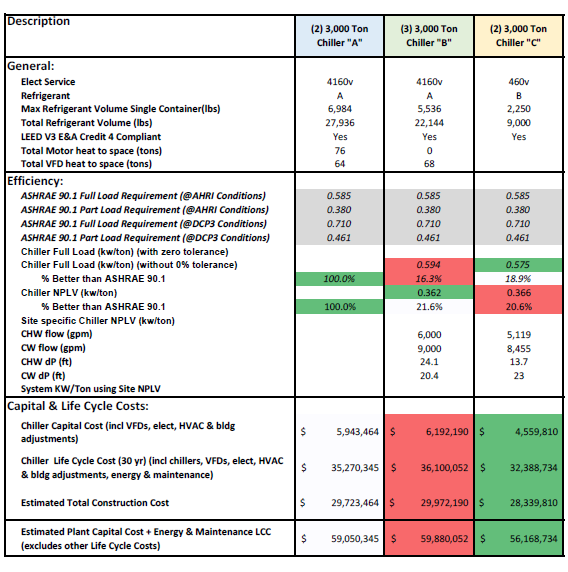
Chiller LCCA Summary
Conclusion
A Life Cycle Cost Analysis is more than just a financial tool; it’s a strategic approach to managing the total cost of ownership for facilities and systems. By taking a long-term view, a LCCA helps facilities managers make decisions that are economically sound, environmentally sustainable, and aligned with the goals of the organization. Eliminating the LCCA process can lead to higher long-term costs, unexpected failures, and missed opportunities for sustainability. On the other hand, integrating a LCCA into the decision-making process helps to ensure that facilities are designed, built, and operated in the most cost-effective and efficient manner possible.
Whether you’re involved in the design, construction, or management of facilities, embracing the Life Cycle Cost Analysis process is essential for ensuring the long-term success and viability of your projects.
Have any questions or want to learn more? Shoot us a message at info@eeace.com!