Fluid system hydraulic modeling is an invaluable resource for the designing of new hydronic systems and assessment of existing ones.
For new system design, hydraulic modeling can assist with:
- piping network layout and sizing,
- pump sizing,
- expansion tank and make-up settings,
- control valve sizing, pump control strategy optimization and
- estimating annual energy use.
When modeling existing systems, the tool can be used for:
- troubleshooting problems,
- analysis of “what-if” scenarios, and
- planning for future system modifications.
This process involves developing a software model of a physical hydronic system. The software model incorporates both physical system characteristics (fluid properties, piping material, condition, and geometry, elevation, valves, fittings, coils, heat exchangers, control elements) and operating characteristics (make-up pressure, flow demands, pump curves and speeds, equipment pressure drop curves). After the model is created, operational scenarios can be tested to determine predicted flow rates, pressures, piping velocities, pump horsepower, and equipment pressure drops, among other data. For existing systems, the model calibration process is key. Model calibration confirms that the software model is an accurate representation of actual system performance. To do this, real-time operational data of the physical system is obtained and correlated to the results of the model (system flows, pump differentials and speeds, static and differential pressures). Often during the calibration process, unexpected results reveal unknown issues in the system. Significant pressure drops in systems due to debris deposits, partially closed valves, and poor fitting arrangements have all been identified in model calibrations.
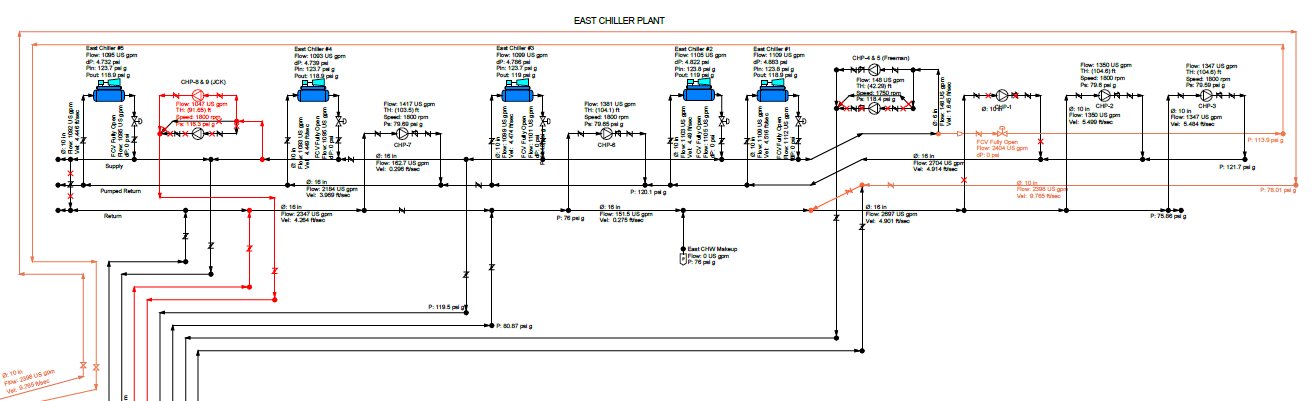
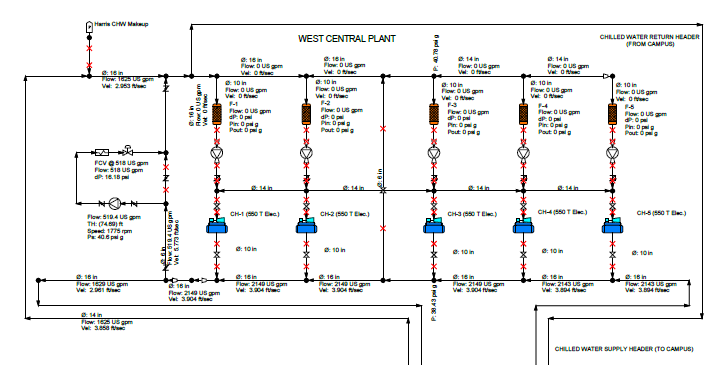
EEA recently used hydraulic modeling for an industrial project with a large process chilled water system. No downtime could be allowed for the system, so project phasing and keeping redundant equipment online were critical components for success. A hydraulic model of the system was built, calibrated to actual conditions, and then utilized to evaluate various phasing, line stoppage, and pumping strategies that would be needed throughout the renovation. The model was also used to evaluate future additional loads and determine if upsizing of the existing pump impellers would be adequate, or if full pump replacement was needed.
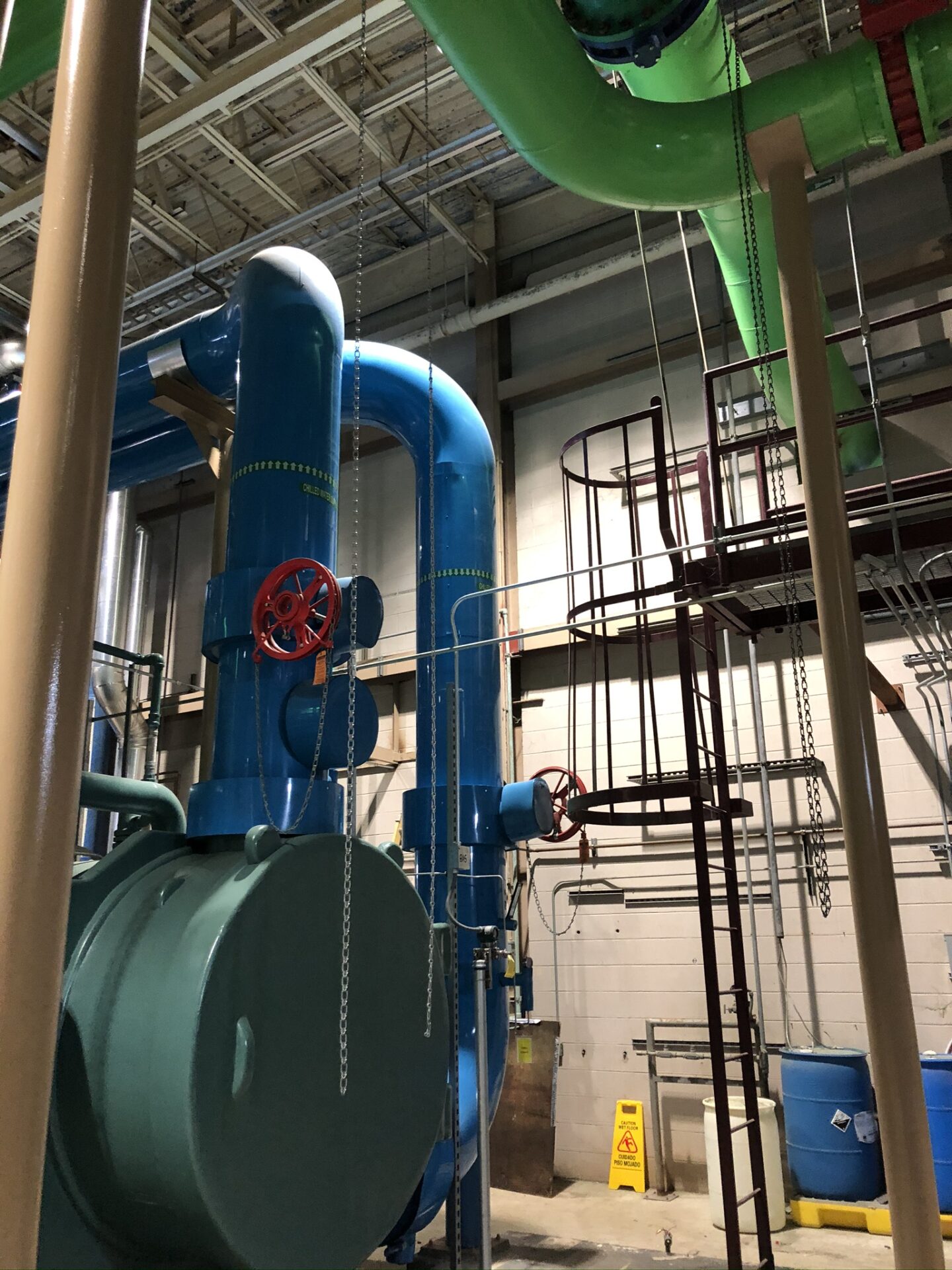
Another previous effort modeled Texas State University in San Marcos’s chilled water system and included over 60 connected buildings, 4 thermal utility plants, and 4 miles of distribution piping. The initial generation of the model required painstaking reviews of 50 years’ worth of buried piping record documents, existing equipment submittals and performance data, and walk-throughs of all building mechanical rooms to ensure accurate geometry was reflected in the model. The calibrated model was used by the campus for over a decade through several system studies and master planning efforts. Some of the “what-if” scenarios tested with the model included line outages and backfeed scenarios, future building additions, plant vs. building pumping usage, and the addition of a 5th thermal plant. Access to the hydraulic model gave the operators a test bench for these scenarios in lieu of live system manipulation, which could potentially result in service issues on campus.
Check out the complete Texas State Hydraulic Model Assessment below:
For more information on how hydraulic modeling could benefit your project, please e-mail us at info@eeace.com.